 |
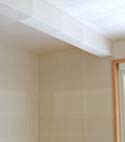
The
"fukuro-bari" on the ceiling and walls are dry now. Next comes
the top layer "uwa-bari".
It requires quite a skill to smooth the soft paper, applied
entirely with glue, perfectly straight on the ceiling. The
washi made in "nagashizuki" style, (discharge papermaking
method) can be peeled and re-hung, with its rough fibrous
texture. Periodically checking whether it is aligned in a
straight row, the papering process continues. |
 |
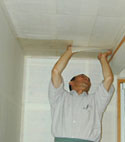
The finished room. The walls are not completely white. The bottom layer can be seen through, and the washi's uneven fibrous texture can be vaguely seen. This is the beauty of "fukuro-bari." |
 |
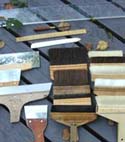
Brushes and smoothers / scrapers. Widths of the scrapers are different for each purpose. To cut washi (mizu-kiri), water is applied with a brush and holding down with the edge of a scraper, washi is gently pulled and torn. Both edges will have untrimmed or fluffy edge similar to "mimi-tsuki" edges caused by the fibrous texture. The handles of the scraper are cut short to fit well in the hands of the paperhanger. The "craftsmen" skill actually begins by knowing how to make his personal tools.
|
|
|
The washi paper have all dried overnight. Today's work entails hanging the top layer or the "uwa-bari". I had specially selected the paper for the top layer in advance. The paper I chose is called "Kohya-Washi" made by an old woman working in a paper mill at the foot of the Kohya-san mountain. I was attracted to her handmade washi for its durability and simple characteristics, and when I heard "the old woman works alone in her mill..." without any hesitation I knew I wanted to use her paper.
Lunch time passed by, and soon dinner time as well. The hanging proceeded smoothly but required more time and labor than anticipated. There are two beams across the ceiling, and the measurement had to be taken to make sure the pattern on the swinging doors of the closet (now removed) aligned with the pattern on the walls. "There is no need to be too particular about details since it is becoming very late" I suggest to the master paperhanger as I peek in the room. He nodded, but it seems that once rules are set, one can not easily change them. This again demonstrates their dedication and I am amazed in the way "craftsmen" adhere to the particulars to accomplish their work thoroughly.
They continue to work late into the night. It is past 11 p.m. and I start to worry, because they had to leave by the end of the day to Tokyo. A little hesitantly, I ask whether I can help in any way. Soon I am in charge of applying glue to each sheet. I pour a little of the hard glue paste onto the glue dish, and add a little water and even out to make a smooth paste. It required more strength than I realized. The youngest woman paperhanger, with the least experience of the four, tells me her muscles ache as she was in charge smoothing out the glue all day yesterday. The clock needles are pointing at 3 a.m. now. At this point, I could not help asking "how long are we going to continue?", the master workman says coolly, "we've come all this way---nothing is going to stop us now".
What was most troublesome was the door to the room. It was originally painted with a dark color, and the surface had decorative uneven patterns on the surface. Because the paper is thin, the color underneath becomes quite visible. We had to figure out how to match the door with the ceiling and walls. What was decided was to paste the under layer directly onto the doors rough surface. After which the top paper can be fixed in the "fukuro-bari" style making the door resemble the appearance of the walls and ceiling as much as possible. The number two apprentices began to paste washi paper tightly onto the door making sure that the paper was glued from every direction of the patterned surface below. Precise and special attention was given to make sure the paper was glued tightly around the doorknob and keyhole. They must have been exhausted after working a full day, but they continued with the arduous work until daybreak.
Not able to keep my eyes open any longer I left to take a little nap, while the workmen carried out the project throughout the night. When I woke up, they had finished the last coating. The coating "kon-nyaku" glue (produced from tubers of Konnyaku root or devils tongue) applied over the surface prevents the washi paper to become dirty easily, and works as an adhesion to avoid the paper to become fluffy.
Usually, I do not like people to smoke, however, when I saw the master smoking a cigarette content with his finished job, I must say the cigarette looked rather good. The new day that greeted us was a very clear day, and we had our late breakfast at 10 a.m.
The four experts worked through this rush work so willingly. No one would have thought it would continue throughout the night, but as I watch them leave my driveway looking rather pleased with what they had accomplished, I too smile and am filled with immense gratitude. You often hear that in the architectural and construction world, many judgements and decisions must be made on the "site" on the spot. The task involved in this project was by no means large in scale, a site of 4-and-a-half tatami's, however, there was much excitement and definitely a special experience for me. The four workmen were not talkative, but their eyes stayed busy watching how their teammates were performing. The master while working, looks over his apprentices, and the apprentices make sure to keep their paces together so the work can be carried out smoothly, while pouring every effort to accomplish with perfection their own responsibilities. I can not describe how I was amazed at their excellent teamwork.
Now, if one were to ask me, " Is your wa-shitsu (Japanese room), more Japanese now with washi paper on the wall and the ceiling?", my answer would not necessarily be a "Yes".
To begin with, the room is not a typical wa-shitsu. Wooden floorboards surround the "Ryukyu" tatami and is not the typical room with tatami mats laid out throughout the room. It isn't anymore Japanese than what it looked before, however, there is without a doubt something calm and soothing to the room. In fact, I think the special qualities of the washi will definitely work well on the walls of any western style room.
Looking carefully around the room, the white window and floor window frames made out of white plastic, seem to stand out. In addition, the reddish wooden frame and the floorboards do not blend too harmoniously. There is still more work to be done to this room. While I am at it, I might even make my own curtain (blind) out of handmade washi.
This year's summer project ended rather successfully and I am most satisfied with how the room looks. My sincere thanks to the four excellent workmen that delayed their summer vacation for this project. Thank you once again. (Yuko Yokoyama)
Photo: Wallpapering tools used: Various brushes, narrow/wide scraper (base smoother/ putty scraper etc.), straightedge measure (with Japanese measurement "shaku" (Japanese feet)),hoshi-zuki(awl),scissors, and utility knife
|
|